Save Time With Cool Grind Coolant Nozzles
Ditch the Loc-Line and PowerFluter! Upgrade your grinding processes with Cool Grind coolant nozzles and experience the benefits of better performance, lower costs, and higher-quality results. These advanced nozzles are designed to replace outdated Loc-Line and PowerFluter systems, delivering unmatched efficiency and precision. Here’s how Cool Grind coolant nozzles can transform your workflow:
- Reduced Wheel Consumption: Save on costs and time by consuming significantly fewer grinding wheels per year, thanks to optimized coolant delivery and reduced wear.
- Lower Coolant Requirements: Cut your coolant capacity needs by up to 50%, reducing operational costs and minimizing environmental impact.
- Faster Grinding for Higher Output: Achieve faster grind times with enhanced cooling efficiency, allowing for increased production throughput without sacrificing quality.
- Improved Surface Finish: Reduce thermal damage and achieve superior surface finishes, ensuring higher quality in your final products.
- Extended Dressing Wheel Life: Minimize dressing frequency and downtime, leading to longer dressing wheel life and more uninterrupted productivity.
- Enhanced Form Retention: Use harder grade wheels without the risk of burning parts, enabling better form retention and precision for intricate geometries.
Extend The Life of Your Grinding Wheels
While it’s true that you can’t fully maximize every benefit simultaneously—such as achieving both maximum throughput and maximum wheel life—Cool Grind coolant nozzles give you the flexibility to prioritize the trade-offs that best suit your grinding goals. For example, in a recent installation, a customer replaced their Power Fluter system with Cool Grind coolant nozzles and achieved remarkable results. By optimizing coolant delivery, they improved the surface finish, delivered a higher-quality part with fewer thermal defects, and reduced the grinding time for a corner radius endmill by an impressive 19%, significantly boosting productivity. Even more impressively, these improvements were achieved without any changes to the dressing or wheel-sticking cycle, preserving wheel life and minimizing downtime.
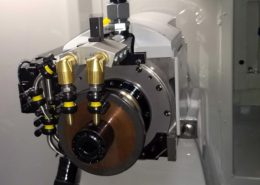
ANCA FX solutions
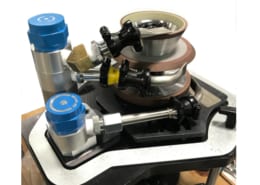
ANCA MX solutions
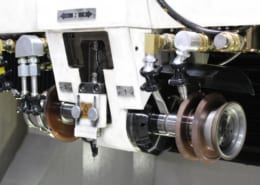
2-spindle WALTER options
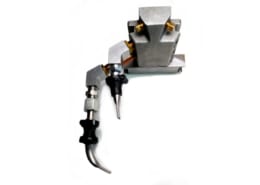